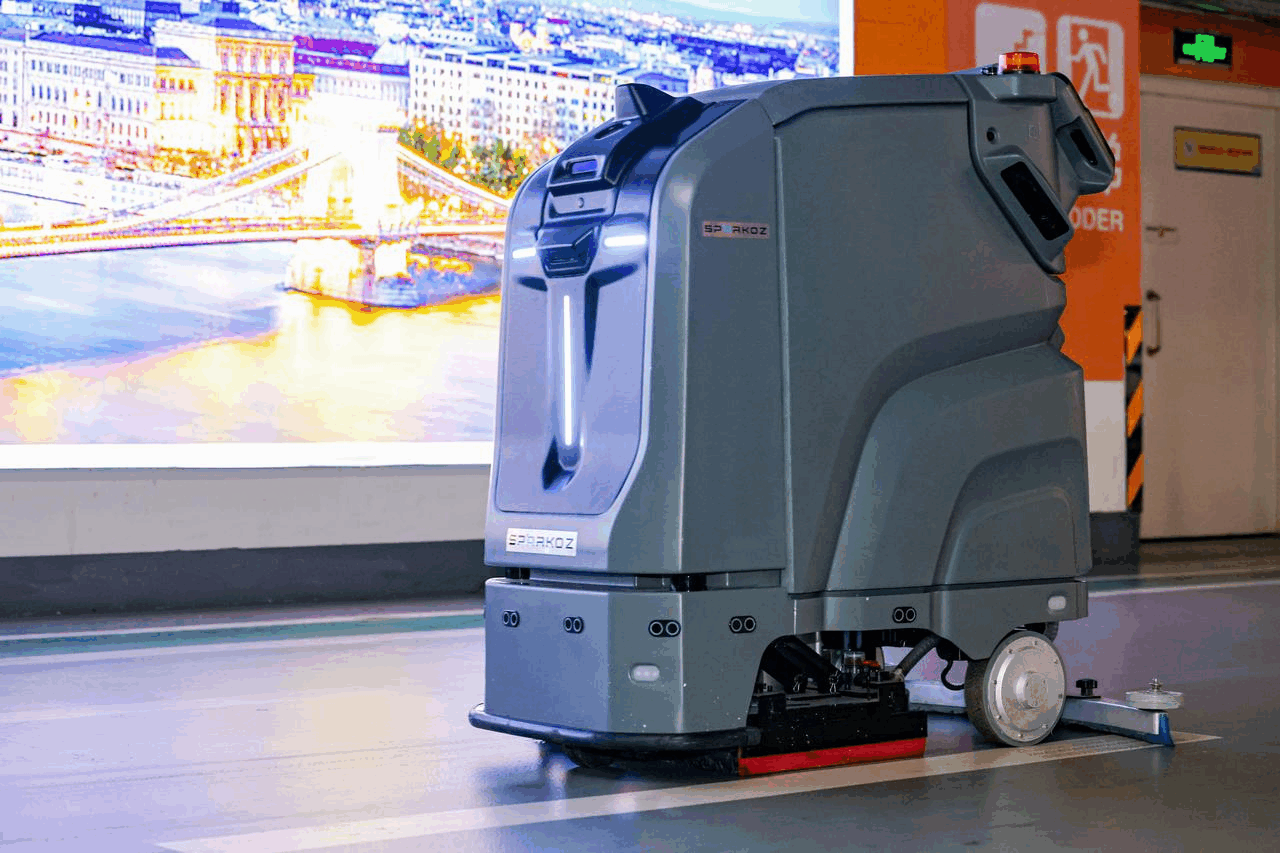
The Evolution of Autonomous Cleaning:Why AI Navigation Matters
The journey toward autonomous industrial cleaning robots is a story of innovation born from necessity. In the early 2000s, the first generation of robotic cleaners emerged, relying on rudimentary random path algorithms or magnetic tape markers to navigate. These systems, while novel, were plagued by inefficiencies: they bumped aimlessly into obstacles, missed entire sections of floors, and required constant human supervision. Fast-forward to today, and the stakes have skyrocketed. Commercial spaces like airports, warehouses, and hospitals demand not just cleanliness, but precision—floors must be spotless without disrupting 24/7 operations, labor shortages loom large, and hygiene standards have become non-negotiable in a post-pandemic world.
Traditional robotic cleaners, dependent on physical markers like wall stickers or pre-programmed routes, are ill-equipped for modern challenges. In dynamic environments—think bustling supermarkets with shifting inventory or airports with rolling luggage carts—these robots quickly falter. They freeze when encountering unexpected obstacles, circle redundantly in complex layouts, and require manual remapping for minor environmental changes. The result? Wasted time, missed cleanings, and hidden costs from human intervention. A 2022 study by the International Facility Management Association revealed that 68% of maintenance teams using legacy robotic systems spent over 10 hours weekly troubleshooting navigation issues, negating the promised efficiency gains.
Enter AI-Powered Navigation:The Brain Behind the Brawn
AI navigation is the tectonic shift redefining what's possible.By integrating LiDAR (Light Detection and Ranging), 3D Time-of-Flight(ToF)sensors, and 360°panoramic cameras, modern robots like Sparkoz's solutions perceive their surroundings with human-like spatial awareness—but with machine precision. LiDAR creates real-time 3D maps by pulsing laser beams to measure distances, while ToF sensors detect subtle depth variations,crucial for spotting low-height obstacles like cords or fallen merchandise. Panoramic cameras add a layer of visual context, identifying surface types (e.g., tile vs. carpet) and adjusting cleaning modes autonomously.
What sets AI apart is its ability to learn and adapt. Unlike static algorithms, AI-powered systems use Simultaneous Localization and Mapping (SLAM) technology to continuously update their understanding of an environment. Imagine a robot scrubbing an airport terminal at night: as chairs are moved or construction barriers appear, the robot's sensors feed data into neural networks that recalculate optimal paths on the fly. This dynamic mapping eliminates the need for physical markers, preserving aesthetics in customer-facing spaces while cutting setup time by 90%.
The Hidden Engine:Multi-Sensor Fusion and Edge Computing
Sparkoz's "Never-Lost" software takes this further with multi-sensor fusion algorithms—a technique that cross-references data from 22+sensors to eliminate blind spots. For instance, while LiDAR might miss a transparent glass wall, the ToF sensor detects its presence through depth anomalies, and the camera confirms it visually. This redundancy ensures reliability in edge cases, such as navigating glossy floors or dimly lit warehouses.
But raw data is useless without processing power. Sparkoz robots leverage edge computing, analyzing sensor inputs locally in real-time rather than relying on cloud servers. This minimizes latency—critical when a robot must brake instantly to avoid a sudden obstacle—and ensures operation in areas with poor connectivity, like underground parking garages.
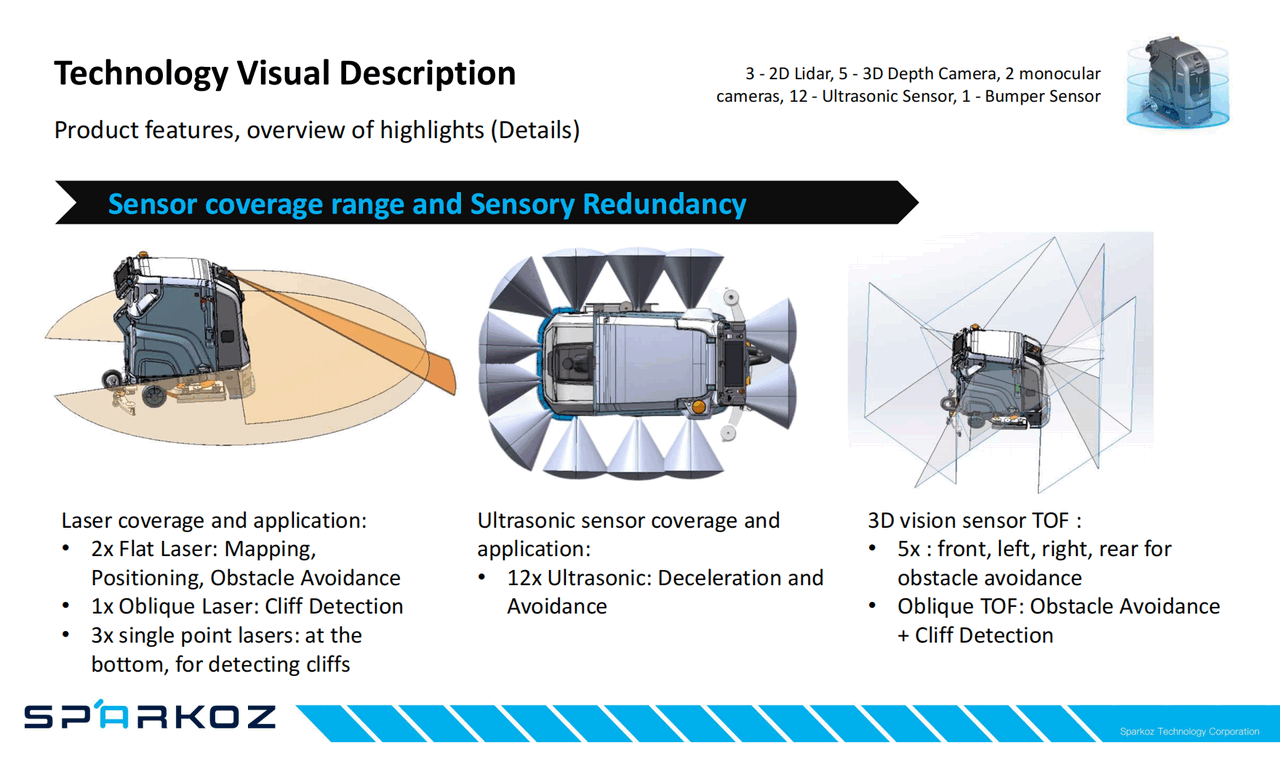
Sparkoz's Leap Ahead
While competitors still rely on QR codes or 2D maps, Sparkoz's encrypted 360°mapping creates a "living" digital twin of facilities. This allows robots to share data across fleets —if one robot detects a spill in a supermarket aisle, others reroute to tackle it immediately. Over-the-air (OTA) updates push new AI models to robots, enabling features like predictive maintenance(e.g., alerting managers about a failing brush motor before it stalls mid-shift).
This technology powers Sparkoz's flagship models, the TN10 and TN70, designed for diverse commercial needs.
1. TN10: Compact Powerhouse for High-Efficiency Cleaning
Ideal for tight spaces like convenience stores or narrow aisles, the TN10 combines a 3-in-1 cleaning system (sweeping, scrubbing, vacuuming) with unmatched agility:
5,000 sq ft/h Coverage: Cleans large areas in record time.
Space-Saving Design: Navigates aisles as narrow as 24 inches.
Digital Management: Monitor robot status, tank levels, and task progress via an intuitive app.
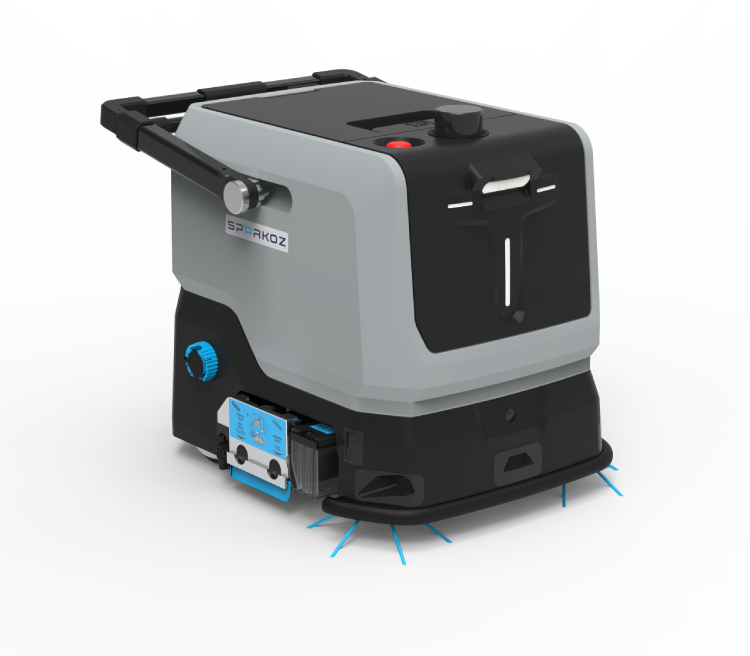
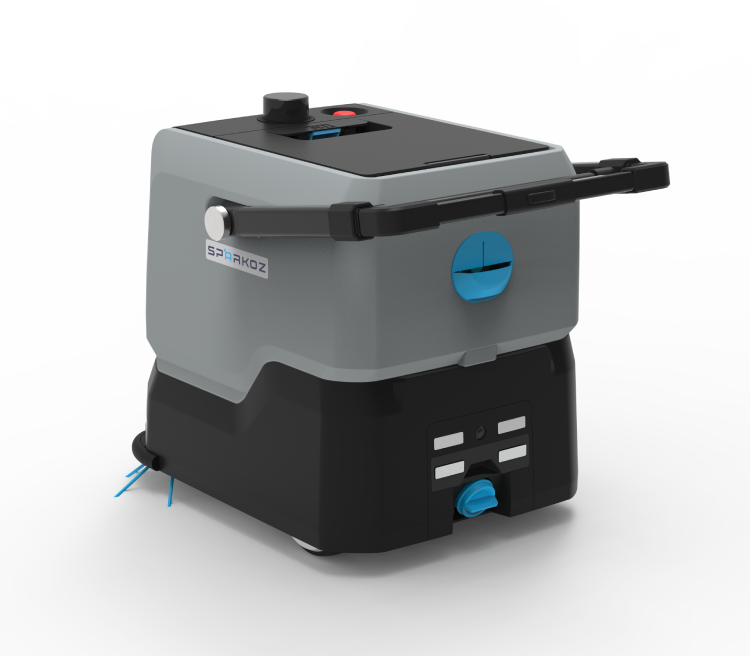
2. TN70: Heavy-Duty Performance for Large-Scale Facilities
Built for airports, factories, and hospitals, the TN70 delivers professional-grade commercial floor cleaning with industrial-strength specs:
70L Tank Capacity&27kg Ground Pressure: Ensures deep scrubbing and zero residue.
2203 m²/h Efficiency: Covers expansive areas at 1.2m/s speed.
20″Disc Brush: The only autonomous cleaning robot with a single brush design.
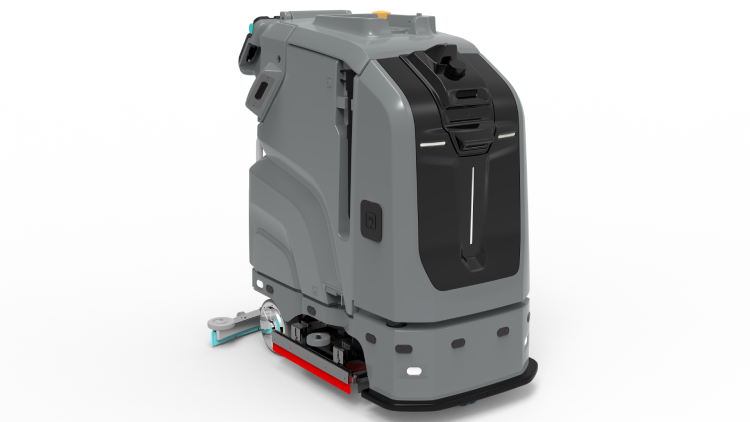
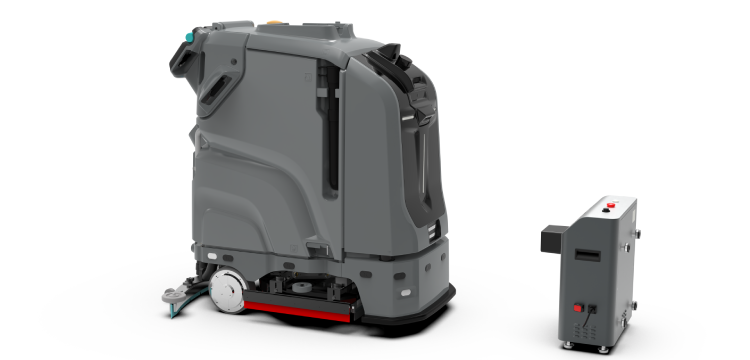
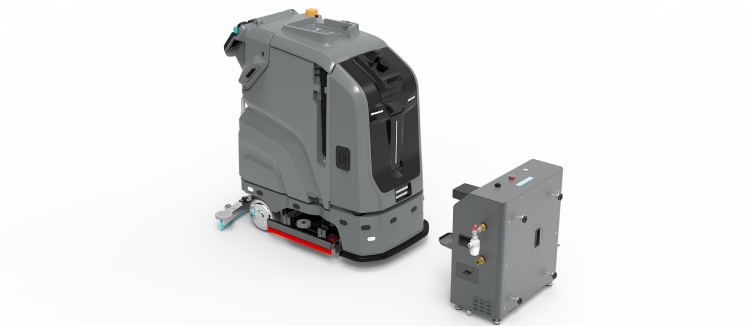
Both models feature Sparkoz's Digital Management Platform, enabling remote monitoring, consumables tracking, and instant fault alerts.
The Future is Autonomous
As AI models evolve, so will their capabilities. Future Sparkoz robots may use digital twins to simulate cleaning routes during facility design phases or integrate with IoT systems to clean high-traffic areas post-occupancy sensors detect foot traffic dips. The era of static,dumb robots is over. AI navigation isn't just an upgrade—it's the backbone of a new industrial hygiene standard, where robots work smarter, not harder, and facilities finally achieve the elusive trifecta: spotless floors, lower costs, and seamless operations.